As Vice President of Ground Operations at Veho, I bring over twenty years of experience from various corners of the logistics and supply chain sector, including stints at major corporations like Walmart and Jet.com. This diverse background has equipped me with a deep understanding of what makes warehouse operations not just functional—but exceptional.
At Veho, we place the client’s customers at the heart of our operations. This customer-first approach influences every aspect of our operations—from system design to hiring and training to technology implementation. Our ground operations team strives to create seamless and highly positive experiences for every consumer.
When I joined Veho, the company's clear vision and the drive to intelligently scale operations captivated me. The chance to transform the consumer experience in package delivery and returns was a challenge I was eager to take on. Drawing on my experience, I'm now focused on standardizing Veho's processes and scaling our operational frameworks to surpass market demands—so we can make shipping, shopping, and returns work better for everybody.
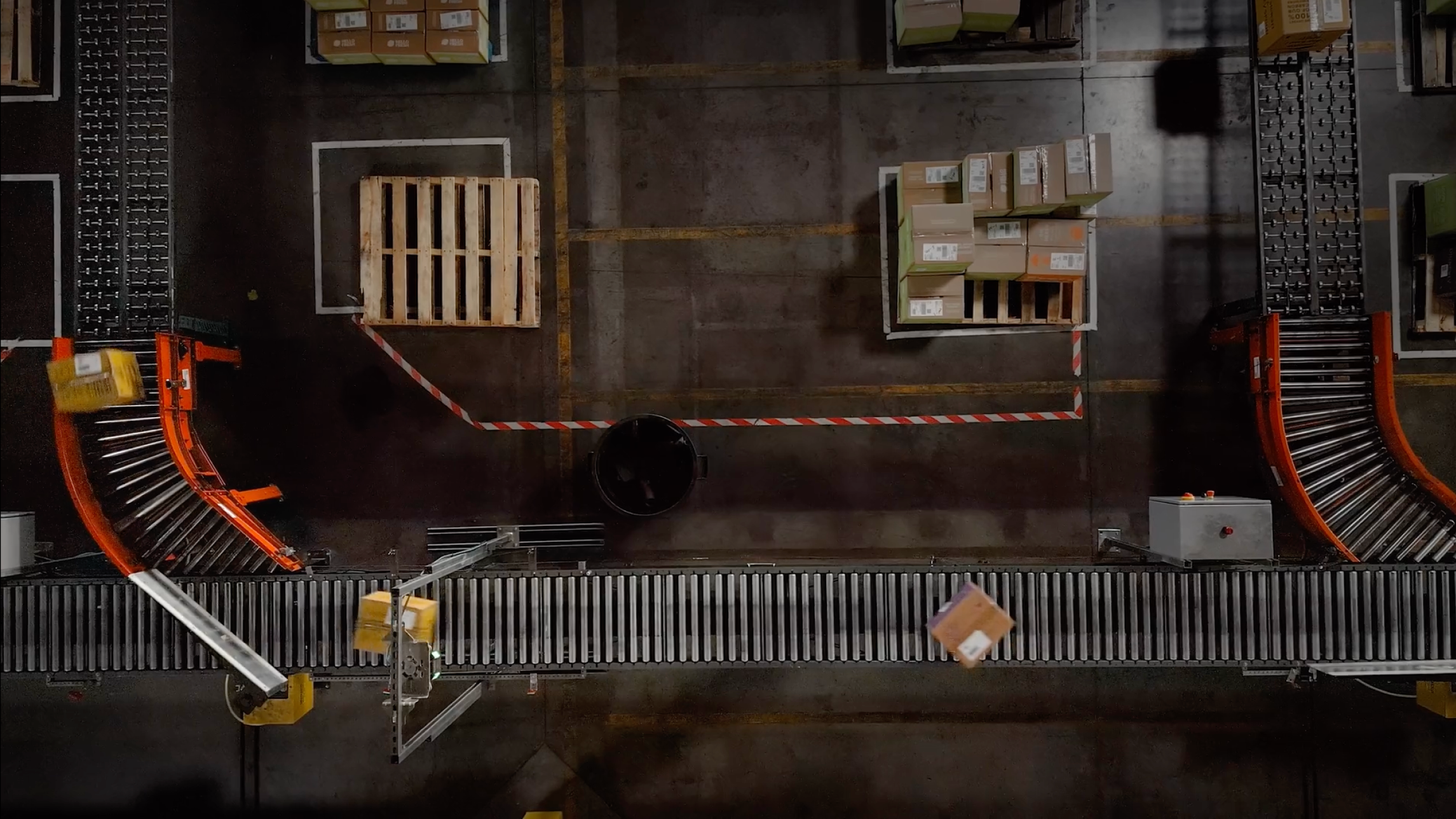
Why Warehouse Operations are Fundamental for Shippers
At its core, the warehouse is the nexus of any logistics system. It's the place where goods transition from the broader supply network to specific delivery routes that end with the consumer. For shippers, the efficiency and effectiveness of warehouse operations directly influence several critical aspects of their business, from the speed of delivery to the integrity of the shipped goods. A well-oiled warehouse operation reduces errors, speeds up shipping times, and ultimately, saves money—benefits that Veho can pass along to our clients.
- Speed of delivery: Efficient warehouse management directly impacts the speed at which products reach consumers. Streamlined processes such as picking, packing, and sorting reduce the time from order to delivery, meeting modern consumers' expectations for rapid service.
- Integrity of shipped goods: Proper handling within the warehouse ensures that products maintain their quality and can be delivered in excellent condition. This minimizes the risk of damage and preserves consumer satisfaction.
- Reduction of errors: Well-organized warehouses significantly decrease the likelihood of errors such as mis-picks or shipping inaccuracies, which in turn reduces the incidence of returns and enhances consumer trust.
- Cost savings: Optimized warehouse operations utilize resources more efficiently, thereby reducing labor, time, and material costs. These savings can make the shipping process more economical and allow shippers to offer more competitive pricing.
- Adaptability to market demands: The ability to swiftly adapt warehouse operations in response to changing consumer demands and market conditions is crucial. Effective warehousing provides the flexibility to scale operations up or down, ensuring consistent service without excessive costs.
Strategic warehouse operations are a top priority for Veho, because it directly impacts our clients’ bottom lines.
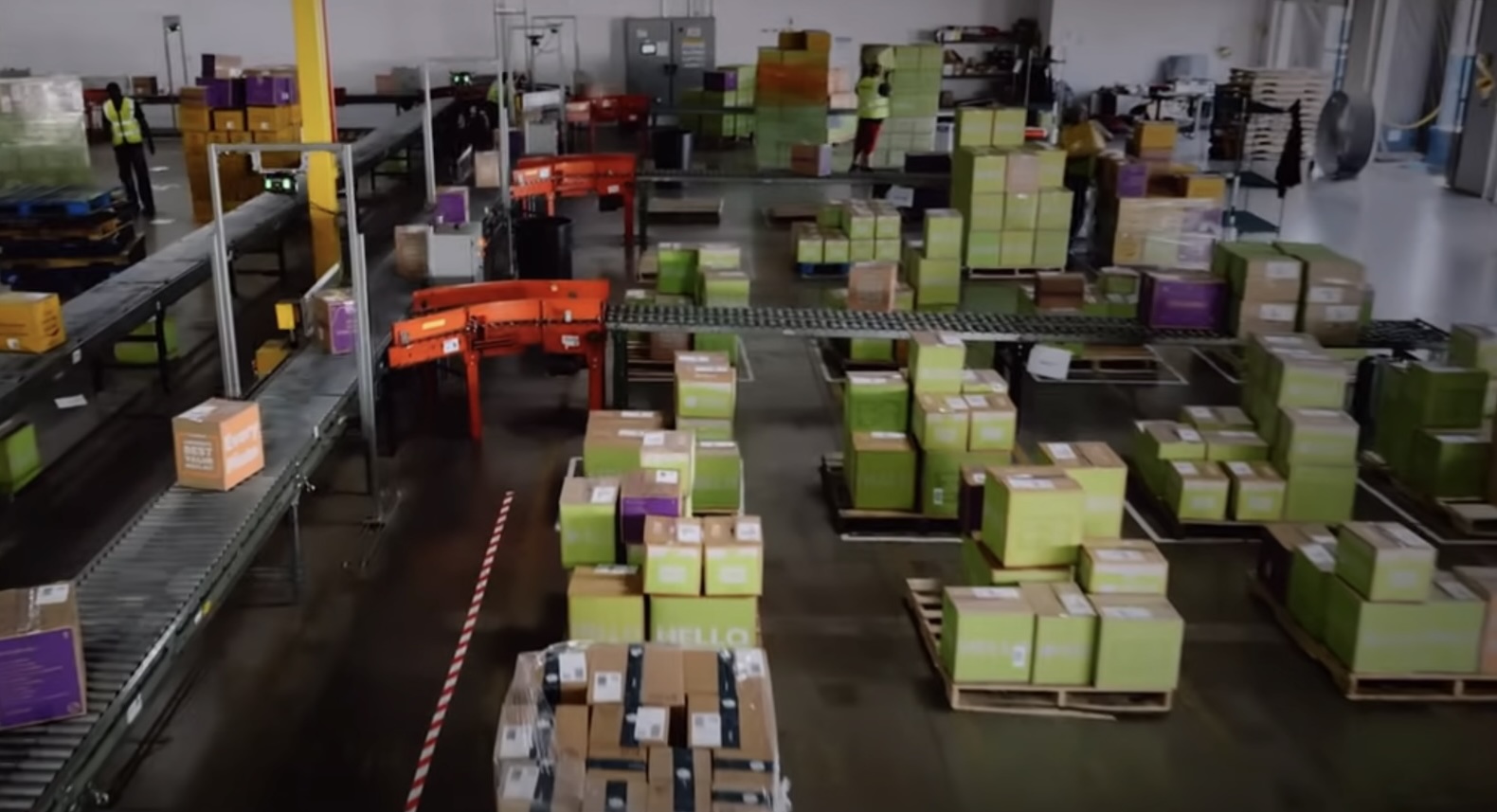
How Veho's Warehousing Operations Differ from the Norm
Veho's approach to warehousing operations diverges from traditional models. Where these traditional models might focus on volume and speed at the cost of customization and flexibility, Veho knows that speed is a given—and prioritizes a tailored, consumer-centric approach—even at the warehouse level. We engage deeply with our client’s customers, offering them an unprecedented level of control and visibility into the delivery process. Consumers can use our app to specify exactly where they want their packages placed (front gate, garage, etc.)—a level of service that traditional carriers simply do not offer*.
The success of our approach also hinges on our ability to hire well within our warehouses. Veho seeks leaders who are both skilled in logistics and also deeply customer-obsessed. This focus on consumer satisfaction empowers our leaders to quickly identify and solve problems. For instance, when faced with unexpected delays, such as a truck breakdown on a critical route, our leaders' ability to swiftly reorganize our already-agile resources and adjust schedules ensures that we still meet our service commitments without delay.
This leadership approach is about fostering a culture where every team member is aligned with the goal of exceeding customer expectations. Our leaders drive this ethos throughout the organization, instilling a mindset of service excellence that makes our warehouse operations exceed the needs of today’s dynamic market environments.
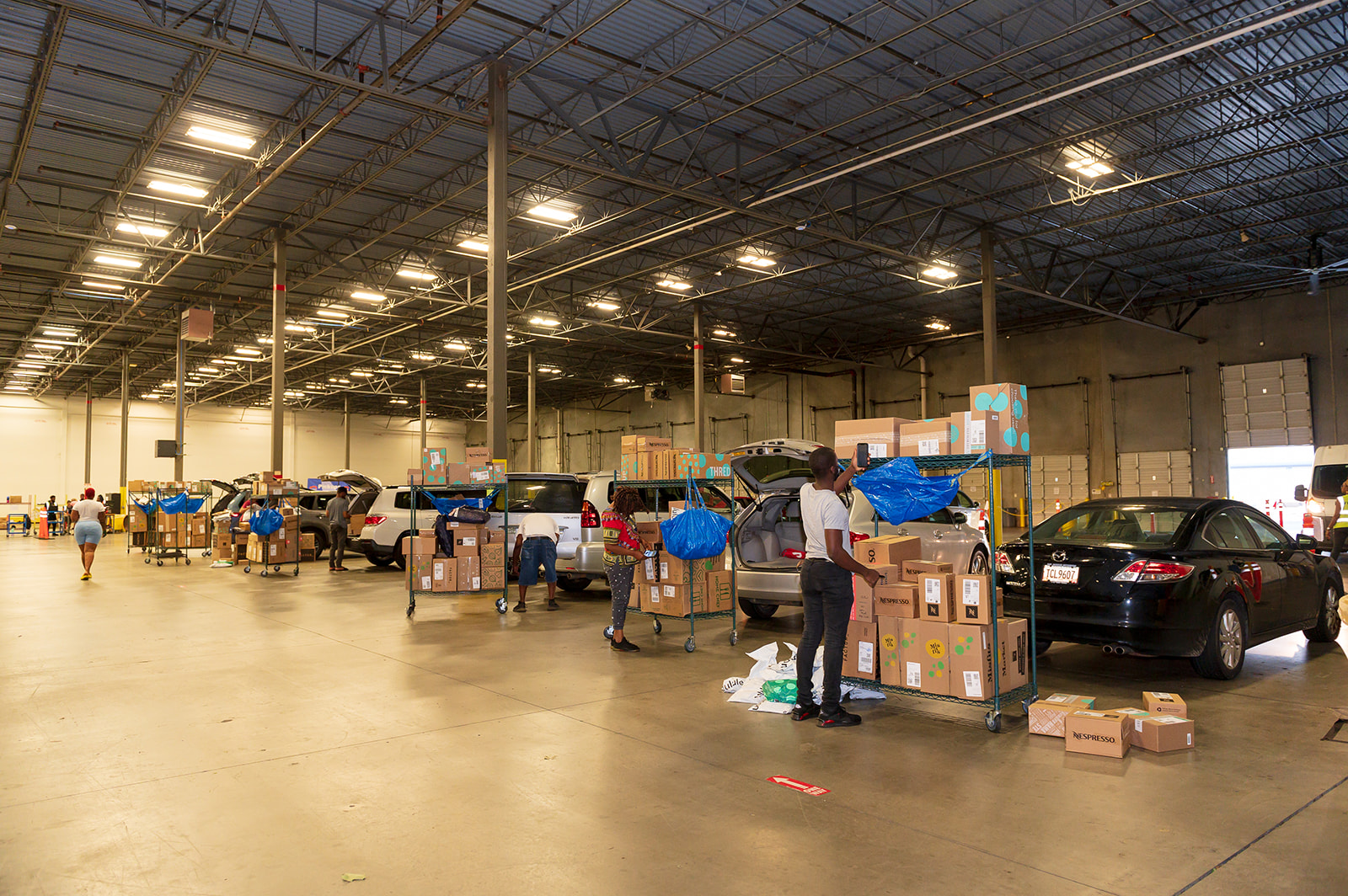
Key Focus Areas for Optimizing Warehouse Operations at Veho
To maintain our competitive edge and ensure the highest level of service, Veho focuses on several key areas to optimize our warehouse operations. These areas, critical for upholding our standards of efficiency, safety, and customer satisfaction, include:
- Safety and Quality Control
- Operational Agility
- Technological Integration
- Continuous Improvement
Safety and Quality Control
At Veho, safety and quality are paramount in our warehouse operations. We meticulously create and maintain a safe working environment, which is crucial not only for compliance and morale but also for operational efficiency. A safe workplace reduces downtime caused by accidents and increases the productivity of our team.
We support safety through clear, easy-to-learn processes and thorough documentation, ensuring that all warehouse workers can quickly master and adhere to our protocols. Regular training sessions and updated safety documents reinforce our commitment, embedding a culture of safety throughout the organization and ensuring smooth, secure operations daily.
Quality control is equally vital. We use precise measures to ensure that every package is correctly handled and dispatched. The accuracy of our sorting and routing processes directly affects our ability to meet consumer expectations and reduce misdeliveries. An example of our commitment to quality is seen in our daily operations where each package undergoes multiple checks. We use scanning technology to track packages. These systems are nimble and we are constantly adding features to improve functionality. Scanning technology that tracks packages from the moment they enter our warehouse until they are picked up by driver partners ensures that a package destined for Boston does not end up on a route to Atlanta. If such an error occurs, the system immediately alerts the operator, allowing for quick correction before the package continues along the wrong path.
Operational Agility
Veho’s operational model is crafted for flexibility and rapid adaptability, allowing us to efficiently manage any logistical challenges that arise. This agility is crucial when facing unexpected situations.
For instance, when a truck traveling from Orlando to South Florida broke down, risking significant delivery delays, our operational team acted swiftly to mitigate the issue. We adjusted the sorting schedule at our South Florida hub to align with the truck's delayed arrival at 2 or 3 PM, rather than the initially planned 6 AM. To handle the backlog of packages quickly, we brought in additional resources and extended our operational hours into the late evening, ensuring all packages were processed and ready for pickup by driver partners by 8 or 9 PM. This is the leadership and problem-solving that Veho strives for.
Additionally, our engagement of independent contractor driver partners allows us to dynamically adjust our delivery capacity. This flexibility includes quickly mobilizing additional driver partners to meet increased demand or reroute driver partners to recover packages on delayed routes. This allows Veho to maintain service continuity and meet delivery commitments even under challenging circumstances.
Technological Integration
Veho is a technology driven logistics platform that facilitates deliveries and returns. Advanced technology is fundamental to Veho’s operations, distinguishing our approach from more traditional logistics models. In our warehouses, the integration of advanced technology ensures precision and efficiency.
Beyond error prevention, our technological framework leverages extensive data analytics to better overall operational decision-making. Each scan generates data that we analyze to track package flows, identify bottlenecks, and optimize routes. These keep packages on the correct route while also gathering valuable data that informs broader operational improvements. This data driven approach sets us apart and allows us to always be improving for our client’s and their customers.
Continuous Improvement
Continuous improvement is ingrained in Veho's operational ethos. We are committed to refining our processes continually, utilizing lean manufacturing principles, Six Sigma, and Kaizen methodologies. This approach to improvement is supported by a robust, data-driven strategy that allows us to monitor performance and adapt as needed.
By analyzing data collected throughout our operations, we can identify areas of waste and inefficiency, develop solutions to address them, and implement changes that lead to more streamlined operations. Our commitment to continuous improvement ensures that we not only meet but exceed the evolving expectations of our clients and their customers, fostering a culture of excellence and innovation in our operations.
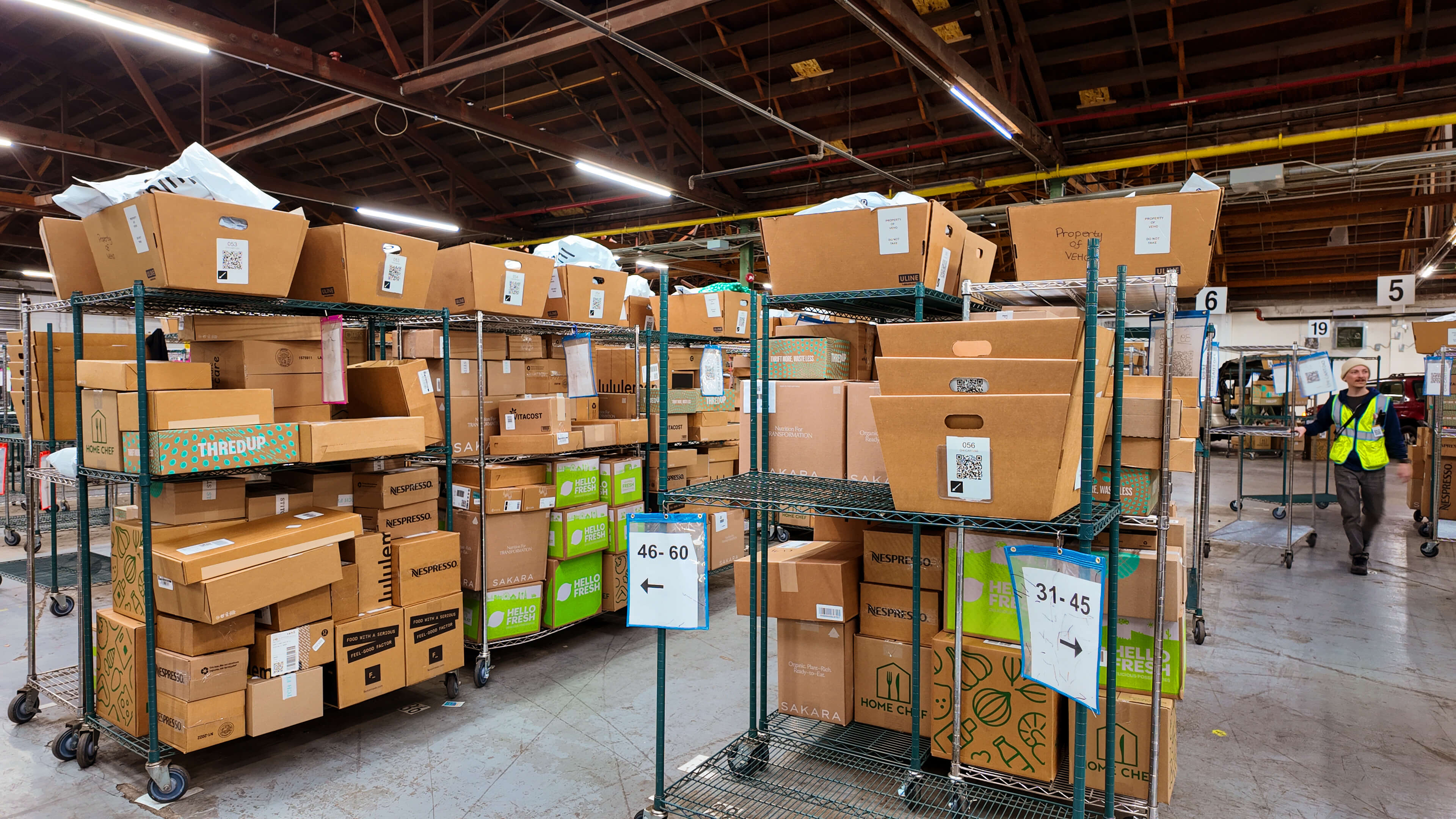
The Future of Veho's Warehouse Operations
Looking forward, the future of Veho's warehouse operations is bright and ambitious. In some of our warehouse locations, we are on the cusp of integrating more advanced automation technologies that will improve our ability to handle packages and enable even more growth for our clients. This automation is set to revolutionize how we handle packages and will feature fully-automated sorting systems—capable of processing thousands of packages per hour, a significant increase over manual capabilities.
Automation promises to lower our cost per package and improve our accuracy and speed, allowing us to handle a larger volume of packages without sacrificing quality for our clients and their customers. These improvements will unlock new levels of operational efficiency and open up possibilities for further expansion and service enhancements.
The foundation of Veho's success in logistics lies in our innovative approach to warehouse operations and technological innovation. As we move forward, these advancements will benefit the countless businesses who rely on us for their logistical needs– and drive growth for our clients.
*Patent applied for